Labour in ‘Amrit Kaal’ : A reality check
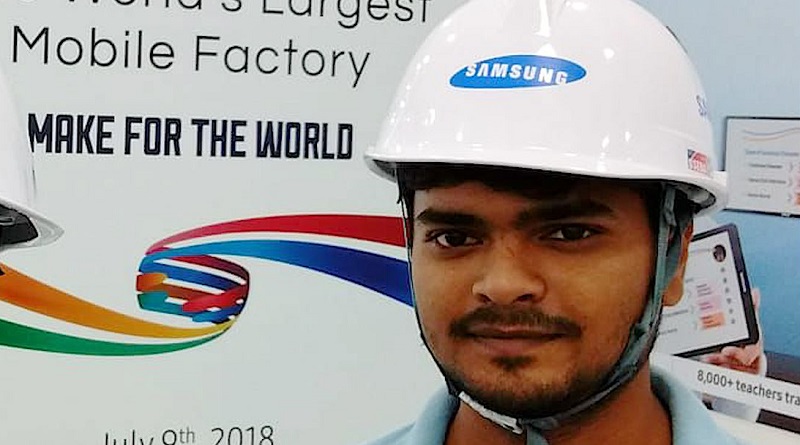
By Annavajhula J C Bose, PhD
Good things are expected to happen or materialise, like manna falling from heaven, during ‘Amrit Kaal’—from India@75 to India@100. In that vein, what could be in store for labour–the working class?
You are concerned because you are academically aware that in “developing countries, labour markets play a central role in determining economic and social progress since employment status is one of the key determinants of exiting poverty and promoting inclusion. Yet the reality in most developing countries is that the labour market fails to create the jobs in the formal economy that would help individuals and their families prosper” (Cazes and Verick, 2013).
As a student of economics, you had found me babbling like a baboon and unable to explain, using the econ texts, how labour is used to make things in the real world. Assume, therefore, that you had gone to do your own ethnographic research–Kafkaesque “investigations of a dog”–at Samsung Electronics India–a huge state-of-the-art manufacturing complex in Noida Phase II, which makes washing machines, televisions, refrigerators and mobile phones. These are the findings (Pratap, 2013) you have replicated and shared with me.
Apprentice workers constitute half the total assembly line production workers, and the other half, regular workers and trainees–those who have completed the apprenticeship. Apprentices are students of Industrial Training Institutes (ITIs). After completing their course, they get a credit for apprenticeship/internship of 1-3 years in the relevant industries. Not more than four per cent of the apprentices is generally absorbed in the regular workforce, and these are engaged first as trainees for two years; and not all trainees are absorbed as regulars. Young women are also significantly engaged as production workers. Majority of workers are migrants from distant districts of Uttar Pradesh.
Also Read:-
- Tamilnadu Factories Amendment bill 2023 has to repeal: Bharathi, LTUC Leader
- Let us be prepared for a new Tamil Nadu Factories Amendment Law!
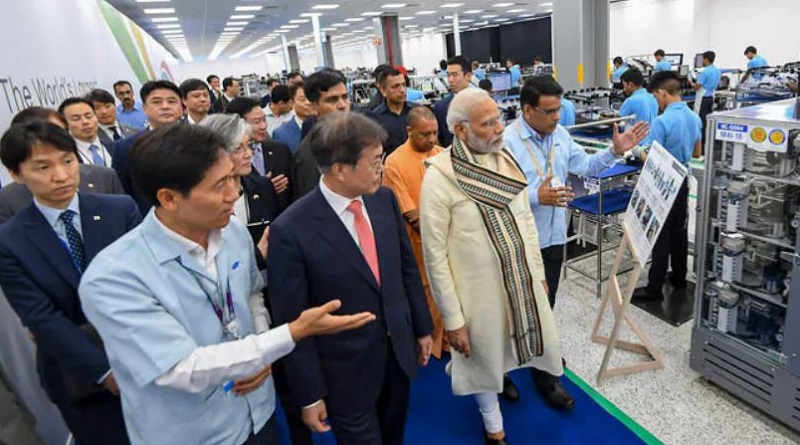
The production/assembly process is highly automated. Production targets for the assembly lines are set by fixing the time taken to complete a specific task, and accordingly the total production target for the day is fixed. Workers in the mobile phone assembly line have to complete their specific task in about 4 seconds. That means, every four seconds one mobile phone is delivered at the end of assembly line. The production process is so hectic that workers have no time or space for doing anything other than their own tasks.
Taking time off to go to toilet or drink water has become a serious problem. As such, workers gradually learn how to avoid going to toilet during work time and how to quicken the pace of work to get time off to drink water while working. But as a result, there are serious health problems like headaches, fever, body pains, exhaustion, nausea and anxiety. Health is also negatively impacted by continuous exposure to ionizing radiations, organic solvents, heavy metals such as cadmium and lead, and to chemicals that damage the reproductive organs, such as arsine and phosphate. In the event of a collective health crisis or mishap, no enquiry takes place and no action is taken by the Labour Department.
Basic wages are Rs 5,800 for regulars (skilled workers) and Rs 5,600 for apprentices. This is after allowing for ESI and PF deductions. With increments, wages of senior regulars increase to about Rs 6,000-7,000. However, the take-home wages, which includes overtime, is much more. Regular workers earn Rs 10,000 to 12,000 or even more, if all the various incentives and overtime payments are included. Apprentices, on the other hand, earn Rs. 7.000-8,000 a month including overtime payments.
The company runs two eight-hour shifts. However, two to four hours of overtime is the general practice, and so both the shifts are of 10 to 12 hours. For example, the day shift starts from 8 am in the morning and can be extended to 8 pm at night. If the targets fixed for the shift are not completed, workers cannot leave the factory. And this happens frequently. Many a time due to increased demand, high targets are fixed while the workforce remains the same, and these targets are completed by increased intensity of work and extended overtime. The rate of overtime payment for regulars is about Rs 80 to Rs 90 per hour, and for apprentices, about Rs 40-Rs 50 per hour.
The assembly line workers are provided with free transport facility and free meals in the canteen. However, these facilities are not provided to contract workers engaged in non-assembly line work. In addition, apprentices are provided with free accommodation for one or two months.
When one joins Samsung initially one feels very peppy and happy because for a few days one is nicely treated by supervisors and the management above. However, after the elapse of only a few days, one feels so bad as never to recommend anyone to join Samsung as the worker is treated, with harsh and abusive language, as a servant and worse than buffalos or donkeys It is difficult to get leave. Since the apprentices are engaged for only one year, they try by all means not to take any leave and to be always in the good books of management, with the hopeless hope that they will one day be regulars. There is no trade union and no system of any other formal representation of workers.
It is clear that Make-in-India companies such as Samsung are adopting the strategy of exploiting apprentices as a source of vulnerable and cheap labour. ITI students are directly recruited from various institutes in various states of India. They are engaged for one year. The whole system is managed in such a way that every two-three months around 150-200 apprentices leave the factory after completion of the one year period and a new batch of an equal number of apprentices arrive in the factory.
Apprentices are offered one-two month’s free accommodation. In the National Capital Region (NCR) of Delhi and surrounding areas, with the expansion of cities and industrialization, many villages have been transformed into colonies where the source of earnings of the landlords of the villages has changed from agriculture to greedy rental-housing.
The landlords have built multi-storeyed housing complexes with a large number of small rooms and with one common toilet for five to 10 rooms. They rent these rooms to low-paid workers. Samsung then contracts with one or two such landlords for 50-60 rooms for one-two months and provides accommodation to 150 to 200 apprentices in these rooms. There is one such workers’ hostel in Barola village, two-three kms from the factory. These hostels are not permanent locations. The company makes new contracts with different landlords and so the location of hostels changes.
Samsung, thus, has a full-fledged system for exploiting the apprentices on a regular, systematic basis. It has also engaged employment agencies for recruiting and supplying apprentices with well-defined terms and conditions. One such agency is SGK India Industrial Services Pvt. Ltd.
In the last few decades, particularly in the industries where the nature of manufacturing operations demands maintaining a larger proportion of regular workers and therefore entails comparatively higher labour costs (e.g. the auto, chemical, engineering and electronics sectors), the trend of engaging contract workers and apprentice workers has emerged and gradually become the norm.
And recently, engaging apprentices is considered much safer and more profitable because they are already trained in some trades; they are legally not considered as workers and so they do not have any right to collective bargaining; they are legally engaged only for one year and so they provide a lot of space for flexible workforce; and they are paid a fixed honorarium and not wages proper. The honorarium fixed by the government for apprentices is very low, far less than the minimum wage, and employers, including Samsung, are actually paying more than the fixed honorarium (near about or equal to minimum wages), and also offering free accommodation for one to two months, free transport and free canteen meals.
Employers are, thus, seeking to engage more and more apprentices as a strategy to use them as a source of vulnerable, low paid, flexible workers. And this strategy avoids trade unionism. Apprentices have to leave the factory after one year, and therefore generally they have no interest in trade unionism.
Also, ITI students are actually engaged not because of their skills in a particular trade. As can be deciphered from the employment advertisements, apprenticeship is offered to ITI students of any trade. ITI students, no doubt, have better skills, but it is their apprenticeship position (short term, low paid worker status) that is attractive to the employers, not their skills and education.
Owing to these advantages, employers have pressurized the government to liberalize or eliminate the rules and laws regarding employment of apprentices, and the government, in turn, has also been more than willing to oblige in the name of promoting skill development among the youth, the future of India.
It is, therefore, not surprising at all to find factories with 100% temps/apprentices. What is surprising is that Indian employers as also government are not at all interested in ushering in ‘amrit kaal’ by way of the European idea of flexicurity—flexibility and security in the labour market whereby employers’ need for a flexible workforce and workers’ need for security are reconciled. Workers do not want to face long periods of unemployment. And government cannot abjure its allegiance to the task of achieving full employment with decent wages.
Your findings of labour exploitation without any overseeing humanistic rule of law as pointed out above, have also been lately vindicated by many labour researchers (see Aggarwal, 2023; Goulart et al., 2022).
If all this labour research does not make us terribly ashamed in dealing with labour in distress, then what will?
(Writer teaches in Department of Economics, SRCC, Delhi University.)
References
Archana Aggarwal. 2023. Labouring Lives. Leftword.
Pedro Goulart et al. (eds.) 2022. Global Labour in Distress. Volume I. Palgrave Readers in Economics. Palgrave Macmillan.
Sandrine Cazes and Sher Verick (eds.) (2013). Perspectives on Labour Economics for Development. ILO.
Surendra Pratap. 2013. Workers in the Supply Chain of Electronics Industry in India: The Case of Samsung. Asia Monitor Resource Centre.
Subscribe to support Workers Unity – Click Here
(Workers can follow Unity’s Facebook, Twitter and YouTube. Click here to subscribe to the Telegram channel. Download the app for easy and direct reading on mobile.)